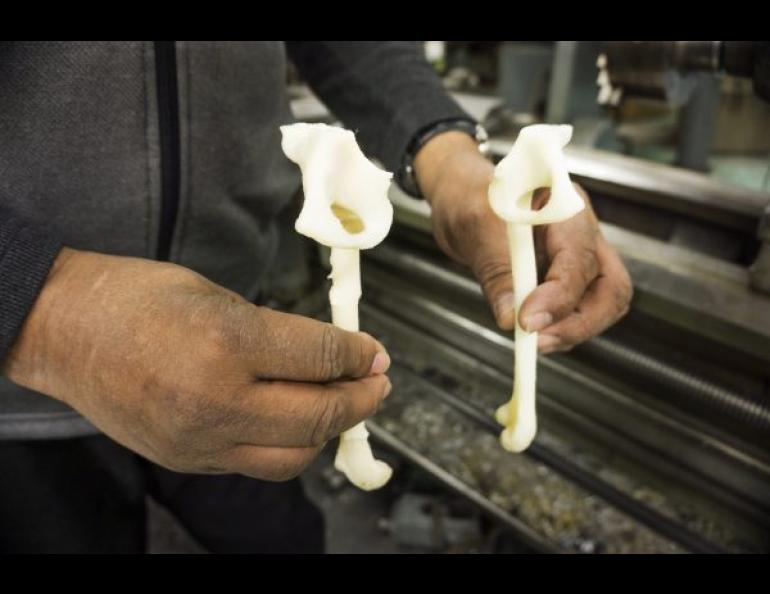
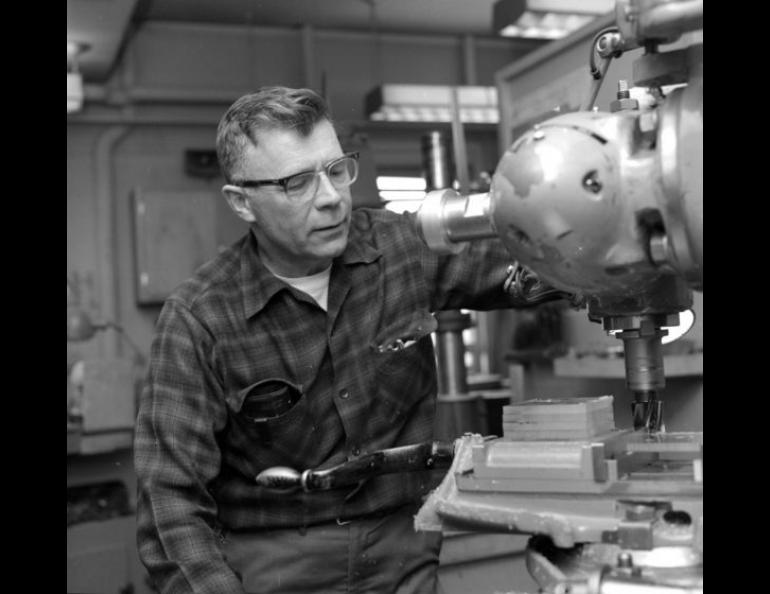
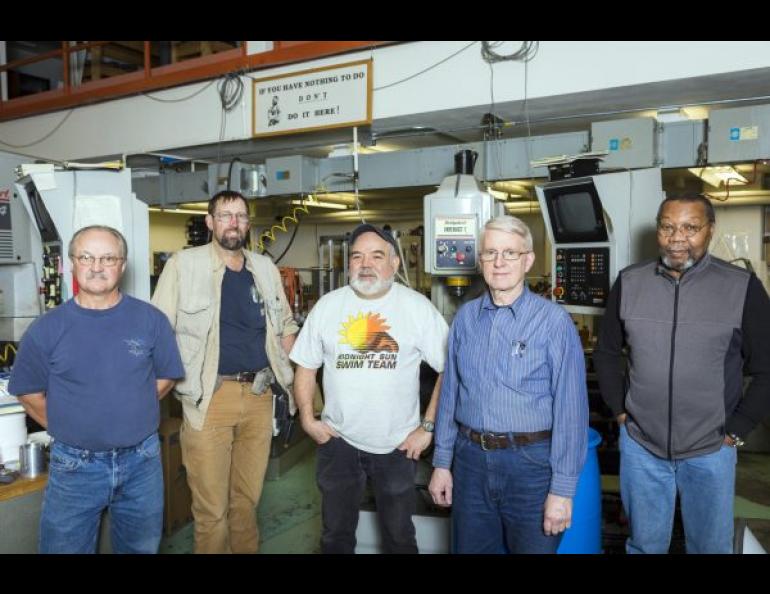
UAF research built upon Machine Shop gadgetry
Download text and photo captions here.
“I never know what’s going to walk through that door,” said Greg Shipman, the shop manager of the Geophysical Institute’s Machine Shop. It’s not an understatement.
Early last year, Fairbanks Memorial Hospital called, asking if the machinists at the University of Alaska Fairbanks shop could make a 3-D print of a broken bone by using MRI scans of a 12-year-old boy’s leg.
Hospital staff said looking at the broken bone with conventional X-rays didn’t give the surgeon enough precision. Shipman agreed to the project, since it would give his crew experience using a new data source with the shop’s 3-D printers.
“We were trying to determine if there was a subtle alignment problem with the broken femur,” said Keir Fowler, a radiologist at FMH. “Sometimes the three-dimensional view of things allows you to get a better conception of how things fit together.”
On “normal” days, Shipman and his crew make extremely precise, custom equipment for GI researchers to use in experiments. They build machines, systems or housings for equipment that might be used by scientists conducting research in Antarctica, on tundra along Alaska’s Dalton Highway, in an airplane, in a mobile lab or on a remote glacier.
They have designed and created systems to use hot water to cut a two-foot opening through two miles of Antarctic ice, and a system to drill a hole to retrieve an ice core for study. In recent years, staff at the Machine Shop have built or modified a number of interferometers, which can make measurements with microscopic precision. The shop is expanding its resources for computer-driven 3-D printing.
“Some of the really critical things Geophysical Institute scientists have been able to discover have been dependent on the Machine Shop being able to make particular instrumentation that you cannot buy,” said Roger Smith, director of the institute from 2000 to 2011.
“The Machine Shop is the heart of creativity for instrumentation. If you’re working in the Arctic, the primary thing you have to have is excellent instrumentation,” Smith said.
This January, a receiver the Machine Shop made was critical to the success of a multi-rocket launch at Poker Flat Research Range.
One project involved launching three NASA sounding rockets, all within an hour. One of the rockets released 50 gallons of water about 50 miles high and 20 miles north of the range.
Using a light radar and telescope system partially fabricated by the Machine Shop, the scientists were able to detect the resulting water vapor. The goal was to determine how large quantities of water could affect the Earth’s upper atmosphere. NASA reported that data obtained from the launches was excellent and will be analyzed in coming months.
“We selected the parts, they built the housing for the device, and they customized the housing so that we had good optical efficiency all the way through,” said Richard Collins, Poker Flat’s chief scientist.
The Machine Shop at the Geophysical Institute has been doing this type of work for a long time. An act of Congress established the GI in 1946. The founding scientists recognized the importance of professional machinists being available to fabricate specialized equipment. A 1949 report from the first director, Stuart Seaton, said that as of July 1, 1950, “there will be available … an instrument shop with machine tools” in the Chapman Building, which was under construction at the time as the GI’s first home.
“We are, in fact, a service center,” Shipman said. “We are specifically here for the scientists, researchers and grad students who work at the GI. We can make something they cannot buy off the shelf or something that they come up with in their head.”
“Someone comes in here with a concept or an idea, we have to turn it into reality,” he said. “That is our main function.”
LJ Evans, University of Alaska Fairbanks Geophysical Institute, 907-474-2737, ljevans@alaska.edu